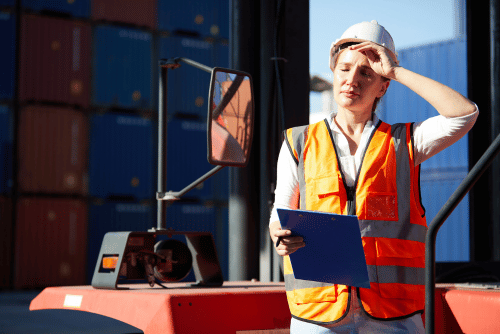
Blog
- Workplace Health & Safety
Home
Resources
Health & Safety
Ikram Mohamed, Senior Health & Safety Advisor
(Last updated )
Ikram Mohamed, Senior Health & Safety Advisor
(Last updated )
As an employer, one of your main responsibilities is to keep your employees, and anyone who visits your place of business safe. Prioritizing health and safety in your workplace will directly impact productivity, employee well-being, and legal compliance. Additionally, the Canadian health & safety legislation requires employers to have a health & safety program in their workplace. This includes having an occupational health and safety (OHS) policy that incorporates safety inspections and safety audits.
While sometimes used interchangeably, safety inspections and safety audits are quite different. In this blog we will explore the differences between a safety inspection and a safety audit, and how to remain compliant with OHS Act regulations by doing both.
The aim of OHSA regulations is to prevent workplace accidents and injuries before they happen. Workplace inspections help to prevent accidents through the examination of workstations, equipment, and facilities on a regular basis. There are two types of workplace health and safety inspections – internal inspections and external inspections.
Your workplace safety inspections should be a part of a larger hazard prevention program, which includes several types of inspections.
Internal and external inspections typically follow a similar approach. External health and safety inspections involve government bodies and external auditors conducting careful assessments of worksites. They are also usually done without much notice, as to maintain authenticity of the findings. The inspector will make recommendations based on the findings, however, infractions and non-compliance could lead to citations, fines, and other penalties.
While a safety inspection provides an overview or routine “check-up” of workstations, workplace audits involve a more comprehensive, thorough assessment of safety performance, policies, and procedures.
Safety audits are critical for providing a detailed look at workplace safety compliance and identifying areas of concern for workers. Some additional benefits include:
Below we have further outlined a few differences between an audit and inspection.
Criteria | Safety Audits | Safety Inspections |
Purpose | Identify critical hazards and rectify them to stay compliant with regulations & standards | Measure the effectiveness of current policies, safety management systems, and procedures, and identify systemic problems & improvement opportunities |
Assessment Scope | Specific areas or activities are targeted to emphasize urgent issues & compliance checks | A complete detailed examination of all aspects of safety management systems, procedures, and policies to pinpoint underlying patterns |
Timing and Frequency |
Predetermined regular schedule |
Typically, unscheduled, and periodic to ensure authentic evaluation |
Personnel involved | Internal staff, supervisors, or third-party safety experts | A team of internal and external auditors, safety professionals, management, and external experts |
Analysis Depth | Superficial examination of specific equipment, tasks, or areas | Detailed and in-depth analysis of policies, procedures, safety management systems and their implementation |
Documentation Focus | Focused on urgent corrective actions and compliance documentation | Focused on documenting findings, recommendations, and ongoing improvement |
Reporting | General report overview based on observed hazards and necessary corrective actions | Detailed report including findings, recommendations, and areas for systemic improvement |
Implementation/Improvement Approach | Emphasis on fixing immediate issues to stay compliant | Focused on ongoing improvement, pinpointing systemic issues, and nurturing a proactive safety culture |
In order to remain compliant with the Occupational Health and Safety legislations and keep your employees protected, it is imperative that you conduct frequent inspections and in- depth audits of your workplace. It is always best if issues arise during these inspections rather than after an accident or injury.
Avoid costly fines for OHSA non-compliance. We can help you pass surprise inspections with ease.
We provide support and expert advice to keep your business health and safety practices up to code. If you have an urgent problem, our certified health & safety advisors will be happy to work with you to solve it. Our experts can also assist you with company policies and with any other human resource management, health & safety, or employment advice you may need. To learn more about how our services can benefit your business, call us today at 1 (833) 247-3652.
Home
Resources
Health & Safety
Find out what 6,500+ businesses across Canada have already discovered. Get round-the-clock HR and health & safety support with Peninsula. Click below to unlock free advice, policies, e-learning, and more.